Lambient Technologies designs and produces instruments for real-time analysis of the curing of thermosets and advanced composite materials such as those used in aerospace, automotive, marine, and wind power applications. Our products offer unique insights into how these materials react and change during curing, processing, and manufacturing. Armed with this critical data, users can proceed with research, quality testing, and final production, confident in the integrity of their processes and materials—and in the reliability of their finished products.
PRECISION CURE MEASUREMENT SOLUTIONS FOR R&D, QA/QC AND MANUFACTURING
STOP GUESSING
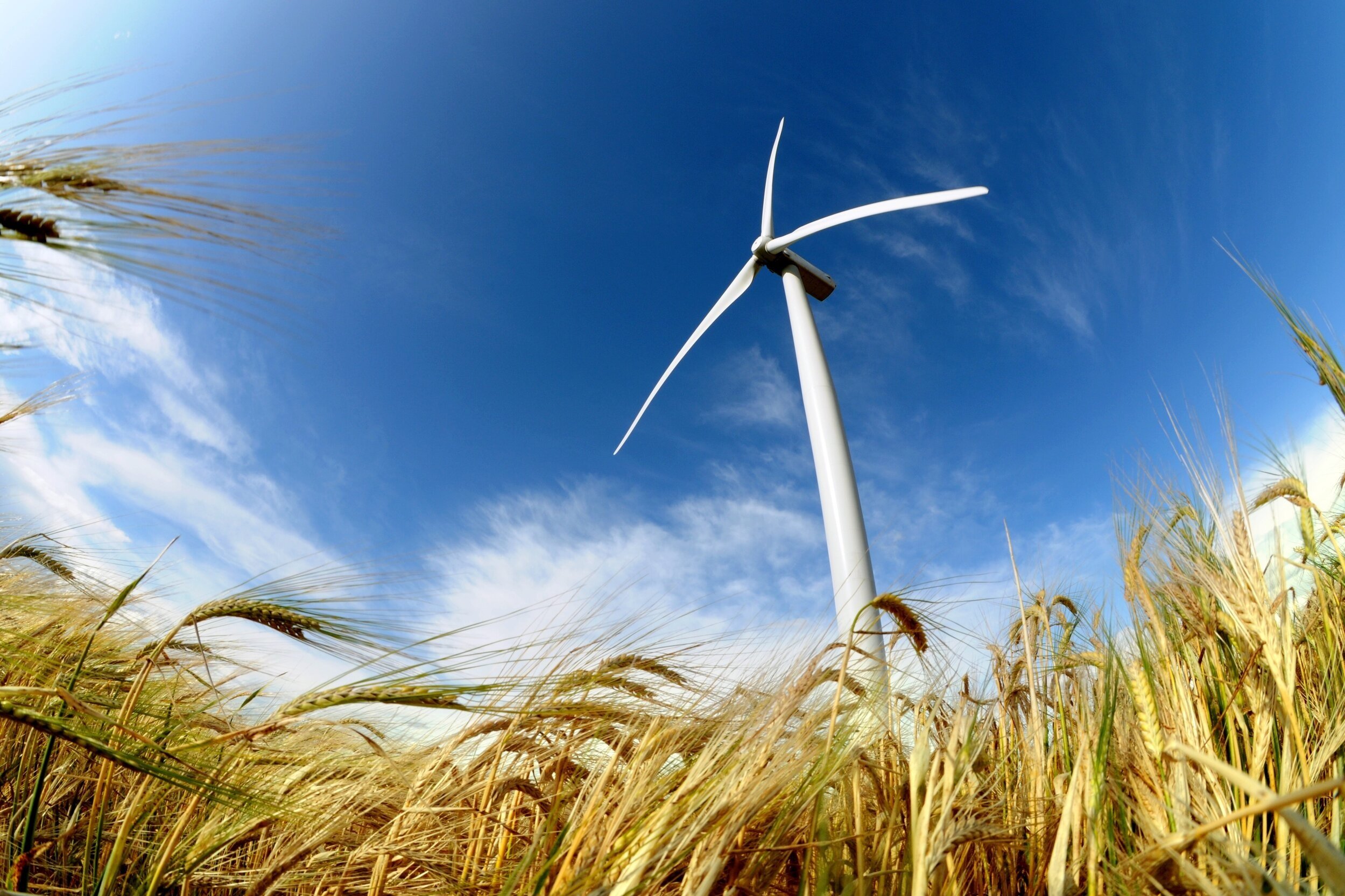